COVID-19 Ventilator
An easy to manufacture and cheap solution to the high demands of ventilators during the COVID-19 pandemic
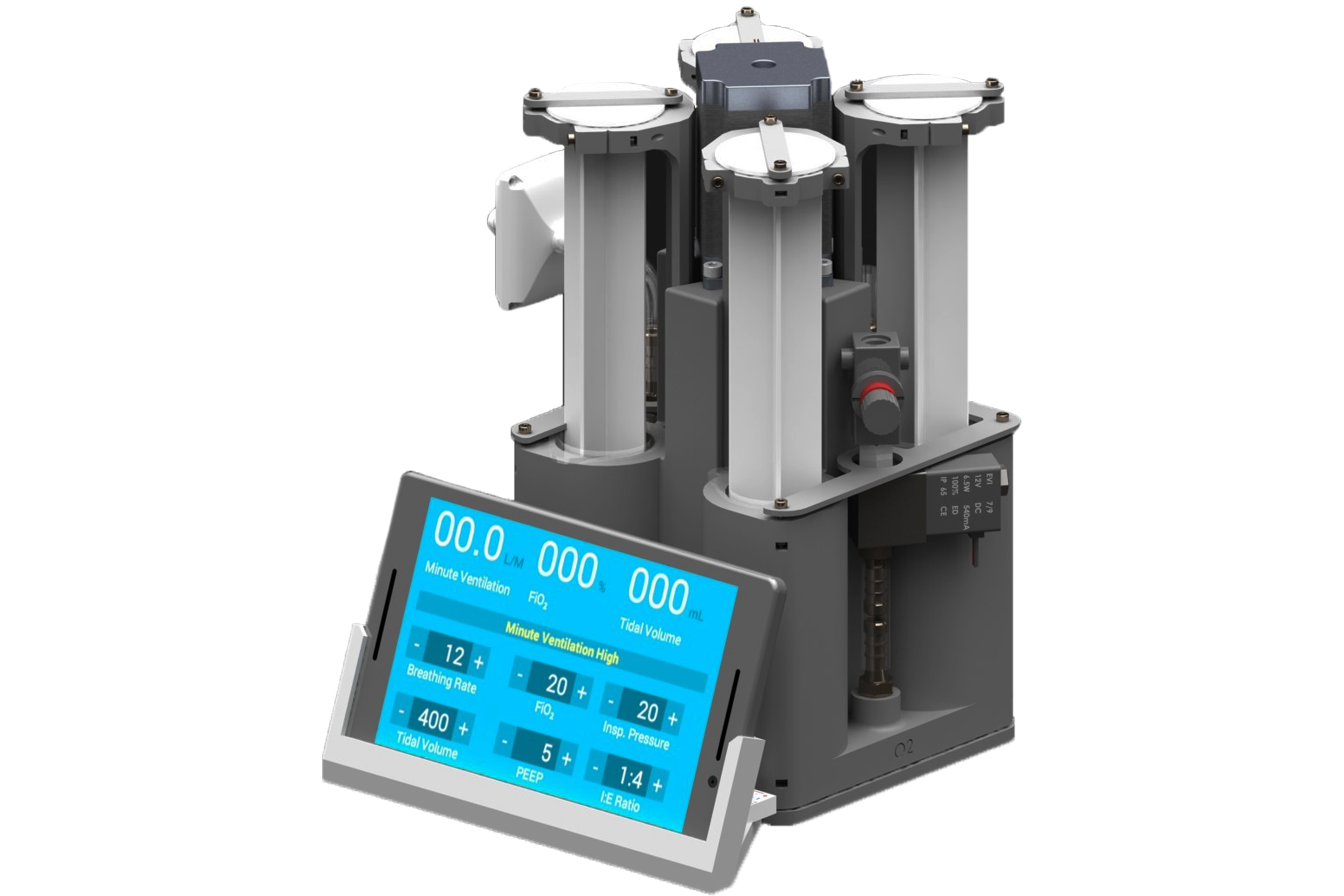
At the beginning of March 2020, it was clear that the COVID-19 pandemic was taking the world by storm. Hospitals were not equipped to deal with the thousands of new cases popping up daily, increasing at a scary rate. During this huge demand for ventilators and medical equipment, I knew I wanted to do something to help, so I found a competition (Code Life Ventilator Challenge) that brought together engineers, medical professionals, and anyone else that wanted to help to come up with a solution to the ventilator shortage. This competition brought together my team of peers from Waterloo, CSA engineers, and doctors from the Ottawa Hospital. Together over the course of 10 days we designed, built, and tested a functioning ventilator, with myself taking a lot of the mechanical design and documentation work.
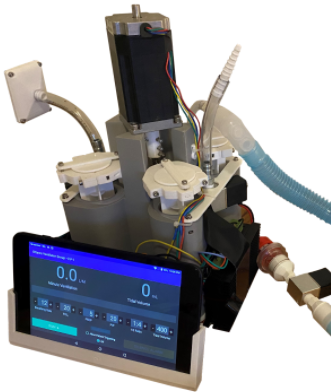
Initially, we did a lot of brainstorming to make sure that we could design a simple and effective solution, we came up with the idea of using large disposable syringes that could be easily replaced instead of sanitizing the entire machine. Then we worked on finding materials we could source in a matter of days, this basically limited our selection to Amazon and McMaster Carr. I worked on designing the airway control paths, this included sealing the syringes, sealing the integrated airways, and connecting the solenoid valves. The final design could pump 600ml of proportionally mixed oxygen and air at a pressure of 40cmH2O into a patient. It could withstand the cyclic loading of 800 breathes per hour in simulation, and had adjustable settings on a simple to use Android app. All the parts were shipped to my house, I assembled it in 12 hours and drove it up to Ottawa to be tested the next day. While it was being tested I helped with documentation, including a simple annotated assembly manual for others to use if they wanted to recreate our device.
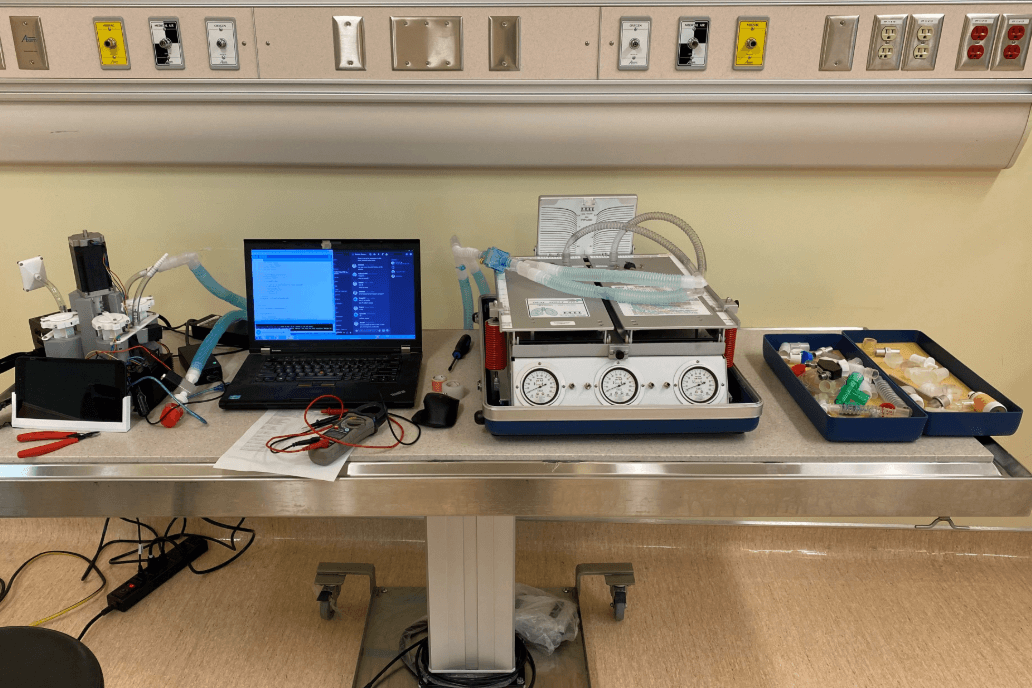
The device was tested successfully with an artificial lung (pictured right) and signed off by doctors at the Ottawa Hospital, but sadly did not qualify to the final round. We were missing a vital part of the requirements; an oxygen sensor, which was extremely difficult to find. Despite this, we posted the files (online) for anyone to access in case they want to build on our progress. Overall I was extremely proud of our team, although we didn’t meet the requirements, we still made something great that had a unique, simple, and effective design.